General Properties
Soundboard: Usually, for the soundboards, soft coniferous woods are in use.The traditional, european material is german spruce. Except in the USA, almost every instrument made before 1960 will be fitted with a german spruce top. In the 1960s, J. Ramirez discovered western red cedar as an alternative to this. This wood distinguishes itself by a very quick response and a somewhat warmer timbre. On the other hand, spruce instruments sound more transparent and are able to produce a larger variety of tone-colours. Recently, North American species such as Sitka-spruce or Oregon-pine, which have already been used in the United States for a longer period, have become more popular all over the world, especially for steel-string guitars.
Back And Sides: As opposed to tops, backs and sides are made from firm to very hard woods. For classical guitars, rosewood has established itself as the standard-material. Here, a decision must be made between Indian rosewood and the variety of South-American species known as Brazilian or Honduras rosewood. I have to say that the tonal differences are very small, and, at least in respect of the instruments´ sound, often don´t justify the sometimes enormous differences in price. Another option is the use of maple for back and sides. It is certainly the tonewood with the longest tradition in occidental culture. Almost every bowed instrument is made with a maple back. With its bright, transparent tone, it is a very attractive alternative to the more mellow Rosewood guitars. Especially for the back and sides, there are a large number of very suitable alternatives available (e.g. Bubinga, Padouk). These have already gained a certain popularity on steel-string guitars. On classical guitars however, these woods still play a minor role, largely because of the more traditional consumers rather than their lack of suitability.
Neck: For the necks, woods with a medium density are preferred. The most important factors are stiffness and a high resistance to warping. For a long period, central American cedar and several kinds of mahogany have proved their suitability. A good alternative wood is alder, which matches the colour of maple better than mahogany.
Fingerboard: The most important property for a fingerboard is its mechanical resistance. For this reason, only very hard woods should be used. For high quality instruments, black ebony has always been the first choice. For instruments of lower quality, rosewood is widely in use. It´s lower density however, often leads to deep hollows between the frets after a few years.
in Common:
Ageing: A major criterion of high quality tonewood is proper ageing. Wood in general is hygroscopic, which means it is able to absorb and evaporate water like a sponge. This is very conspicuous with recently cut-down wood. It easily loses a quarter of its weight during the first weeks of drying. Unfortunately, a quite unpleasant effect occurs: The wood shrinks whilst it dries down, and expands again when it becomes more humid. Even worse is the fact that this happens only transversal to the fibres. This is one of the reasons for those unpopular cracks in instruments tops and backs. Therefore, it is absolutely neccessary to pay great attention to atmospheric humidity during construction. Interestingly, humidity is only one aspect: After a longer period of ageing, the wood “calms” down i.e. it looses its tendency to warp. I guess everybody has at some time observed an industrially manufactured instrument, where the wood was dryed down quickly, and whose neck looks like a banana after a couple of months! Furthermore, there are a number of chemical processes taking place whilst the wood ages, which, e.g. oxidate the resins located in the wood´s structure. So, finally we can state, that proper ageing of the wood is an indispensable factor for the building of fine instruments. Depending on the kind of wood, the ageing process should take from 5 to 8 years.
Cutting: An commomly overlooked aspect in connection with tonewood is the way (or the direction) it is cut. This plays a major role, especially when choosing the soundboard. There are two crucial points relating to this. The first is, that the wood´s fibres run as parallel as possible to the soundboard-plank (“split cut”). With most trees however, this is not possible, because they turn like a corkscrew more or less whilst growing. Secondly, the annual-rings must run as rectangular as possible through the top (“quartersawn”). This can be seen as a transversal structure, the so-called medullary rays. Those cells, running at a right angle to the annual rings are responsible for the board´s transversal stiffness.
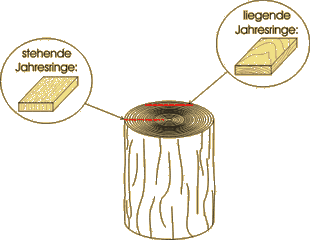
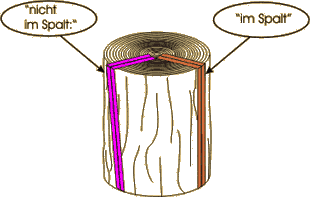
Faults: The decision, what has to be seen as a fault strongly depends on the part of the instrument.The most critical part is surely the instruments top. The soundboard has to be strictly straight grained, without any irregularities.On the other hand an irregularity, such as a knot is not nessessarily disturbing in a back or sides. It can even look very interesting without affecting the sound at all
some of the most frequently used timbers